For efficient shot blasting operation we should understand the basic concept of the process and the machine |
The shot blasting machine consists of six basic parts:
|
1. Blast Wheel
2. Cabinet
3. Work Handling Mechanism |
4. Elevator
5. Separator
6. Dust Collector. |
|
|
Let's take a close look at these six parts and see what role each plays in the shot blasting process. |
|
1. Blast Wheel : |
Abrasive particles are projected by centrifugal force from various kinds of turbine wheels. The number of wheels installed in the machine depends on the type of jobs to be shot blasted and the rate of work. The wheel is the heart of every centrifugal shot-blasting machine. Efficiency and cleaning effect depend to a great extent on the quality of the wheel and its components. |
2. Cabinet: |
As high speed of abrasive particles (50-100 m/s) is involved the articles to be shot-blasted have to be
treated in closed, vibration free booth or cabinet made of strong steel, lined with wear resistant alloy liners. For maintenance purpose proper inspection door and ventilation are essential. |
3. Abrasive Recovery System and Elevator: |
The abrasives are recovered at the bottom of the cabinet by means of a screw conveyor and delivered to the base of the elevator, which then carries these to the separator. |
|
4. Separator: |
Before abrasives enters into the blast wheel for reuse, these have to be cleaned of all contaminants. This is the role of the air separator. |
|
5. Dust Collector : |
The last essential feature is the filtration, which retrieves dust laden air from the separator and cabinet ventilation system and discharges clean air into atmosphere for pollution free environment. |
|
6. Work Handling : |
The abrasives are recovered at the bottom of the cabinet
by means of a screw conveyor and delivered to the base of the elevator, which then carries these to the separator |
Some of the Finish Castings Show below : (Fig-1) |
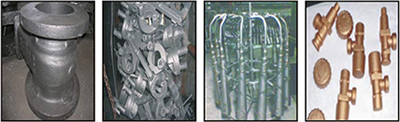 |
|
Tumble Type Machine |
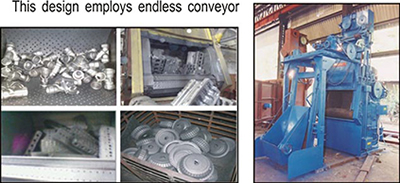 |
|
|
|
belt made of steel link and flats or rubber belt, which does not damage the job during tumbling.
1, 2, 5, 7, 8, 14, 28, 34, Cubic Feet
Capacity : 50 Kg. to 2500 Kg
|
|
Table Type Machine (Fig 3) |
In this type of machine parts being cleaned must be positioned or repositioned on the table to assure complete cleaning of the full surface.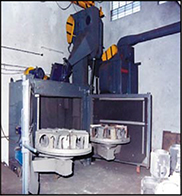
This design employs endless conveyor belt made of steel link and flats or rubber belt which does not damage the job during tumbling
Capacity : (Fig -3)
900 MM. 300 Kg. Approx
1200 MM. 800 Kg. Approx
1800 MM. 2300 Kg. Approx
2400 MM. 4500 Kg. Approx |
 |
|
|
Hanger Type - Y
Straight / Loop / Monorail
(Fig 4) |
In this type of machine, parts are suspended on trees hung on hanger or special fixtures and are carried into the abrasive stream. 2 /3 Wheels Capacity: 2000 Kg. Per Hanger |
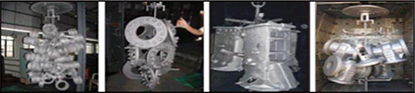 |
|
|
Door Hanger Machine :
(Fig 5) |
In this machine jobs are hung on the door. The parts are carried into abrasive stream after closing the door. The parts are mounted in front of the wheel. On completion of shot blasting, door is opened
1/2 Blast wheel
CAPACITY : 100 / 500 Kgs. |
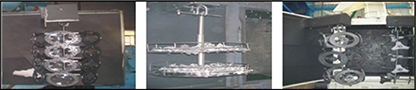 |
|
|
Aluminum Deburring
(Fig 6) |
Aluminum Casting Deburring with shot blasting is the fastest and most economical way to deburr auto components like cylinder heads, |
|
|